Conveyors are essential for automating and optimizing production processes, and they have been a key part of industrial advancements since the early 20th century. Henry Ford is often credited with revolutionizing conveyor systems by introducing the first continuous flow production line for automobiles in 1908. This innovation significantly sped up production and reduced costs.
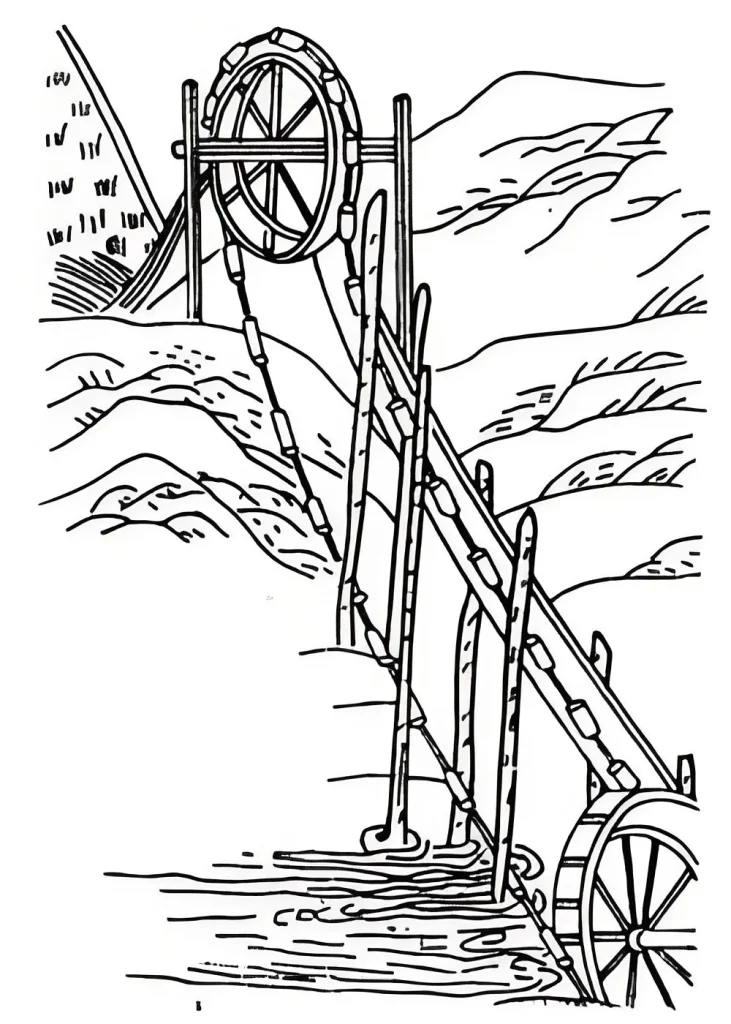
The concept of conveyors, however, dates back much further. In Ancient China, a chain mechanism was created to supply water for irrigation, which can be seen as an early form of the modern conveyor. This early invention demonstrated the ingenuity of ancient engineers in enhancing efficiency and productivity in agricultural work.
The core principle of modern conveyors involves moving an object, such as water or materials, from point A to point B through mechanical means. This principle has been adapted across various industries, from manufacturing to transportation, to automate and improve processes.
Today, conveyors are integral to many industries. Their applications span across various forms and functions, including horizontal, vertical, and inclined transport. Conveyors are essential in assembly lines, sorting, and transportation, handling both bulk and piece goods. Common types include belt, bucket, rope, screw, and roller conveyors, among others.
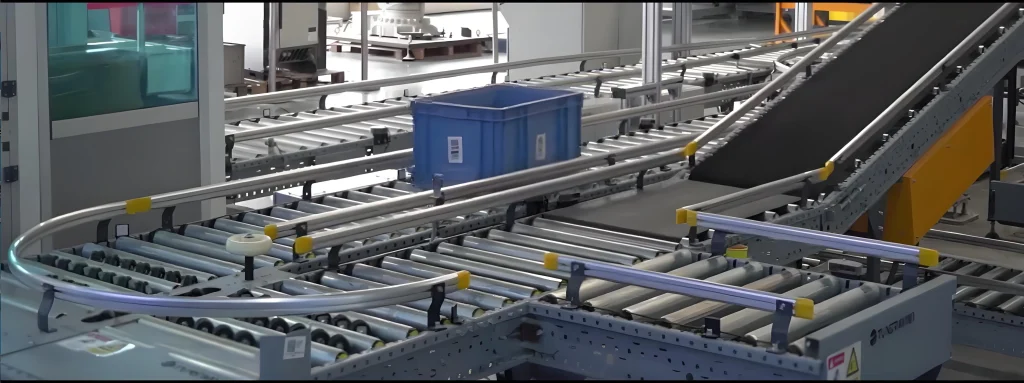
Roller Conveyors and Bearings
Roller conveyors, also known as roller tracks, are among the most widely used conveyor systems. These conveyors consist of rollers mounted on a common frame, over which goods are moved. Roller tracks are used in production lines, postal sorting facilities, warehouses, and even supermarket checkout areas. A single roller conveyor typically contains dozens or hundreds of closely spaced rollers, powered either by motors or gravity. Each roller rotates around its axis on two bearings, and it is the quality of these bearings that largely determines the conveyor’s longevity.
For example, in a postal sorting facility, a single meter of roller track can contain 10-15 rollers, each supported by two or three bearings. With extensive conveyor systems in place, managing the maintenance of so many bearings—requiring constant lubrication, replacement, and repairs—can be challenging. This is where plain bearings offer a highly practical solution.
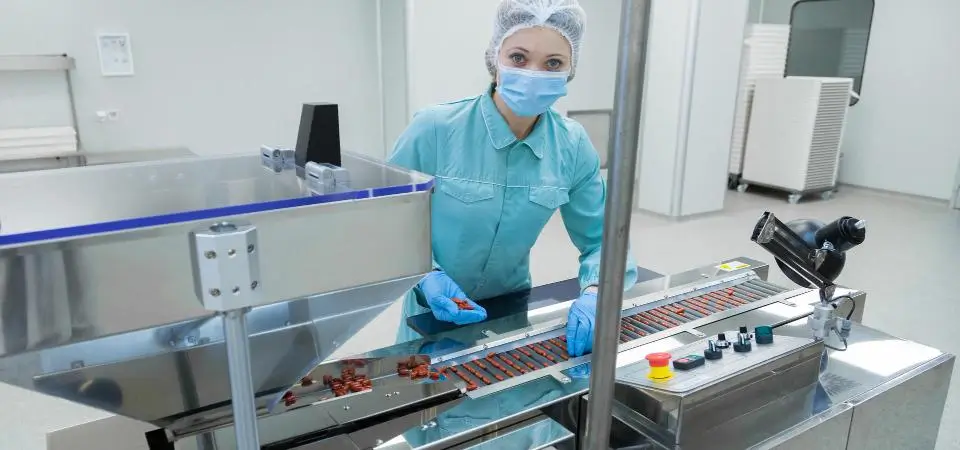